Video gallery
The Manufactory Glashütte Original
The heart of Glashütte Original beats inside the manufactory building: Here, under one roof, thousands of precision components are elaborately produced and assembled with care. In the heart of the town of Glashütte lies a bright and modern manufactory: Glashütte Original. Thanks to our exceptional production depth, we are able to design and produce our timepieces almost entirely in-house.
With over 10,000 square meters of floor space, the modern, generously proportioned manufactory building is a production site and a world of experience at once. The clear structures and transparent materials of the functional architecture reflect the high standards implicit in the “Made in Germany” quality seal. On four floors, corridors link the various ateliers, workshops and departments responsible for production and final assembly.
Glashütte Original upholds a tradition in which handcrafted perfection and select materials are combined with innovative production technologies. As an independent developer and maker of our own movements, we have good reason to call ourselves a “manufactory”. It is an ambitious claim: In the process of making watches here, we still perform a great many critical steps by hand – “per manum”.
Our values
Glashütte Original stands for innovative watchmaking art that meets the highest standards. Our timepieces are the product of the best in German engineering and craftsmanship: technically sophisticated, reliably precise and timelessly beautiful. Clearly defined values play a major role – they give us motivation day after day.
Traditional features of Glashütte watchmaking in perfect harmony
It is an almost magical moment when the individual instruments of an orchestra unite to form a symphony, and passion, intuition as well as a lifetime of practice find expression in a unique sound. In the Glashütte Original ateliers, the finest watchmaking skills, and traditional manufacturing techniques merge with the same dedication to create consummate mechanical timepieces with an uncompromising commitment to precision and beauty. Discover the typical features that distinguish a Glashütte Original watch. Follow us on a journey that will let you experience time like never before.
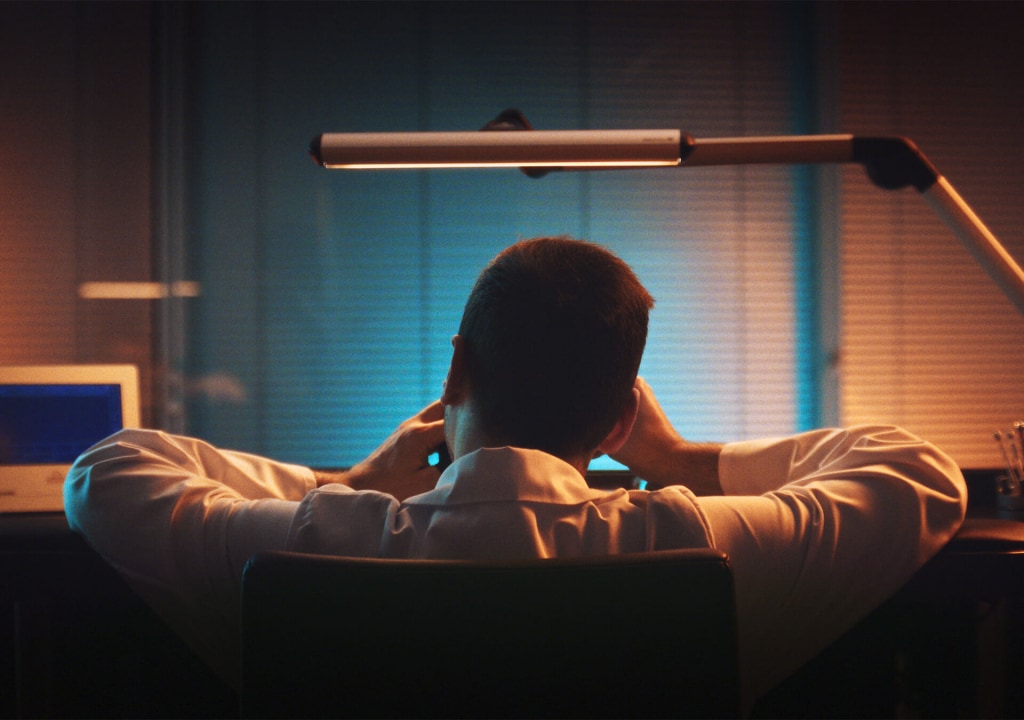
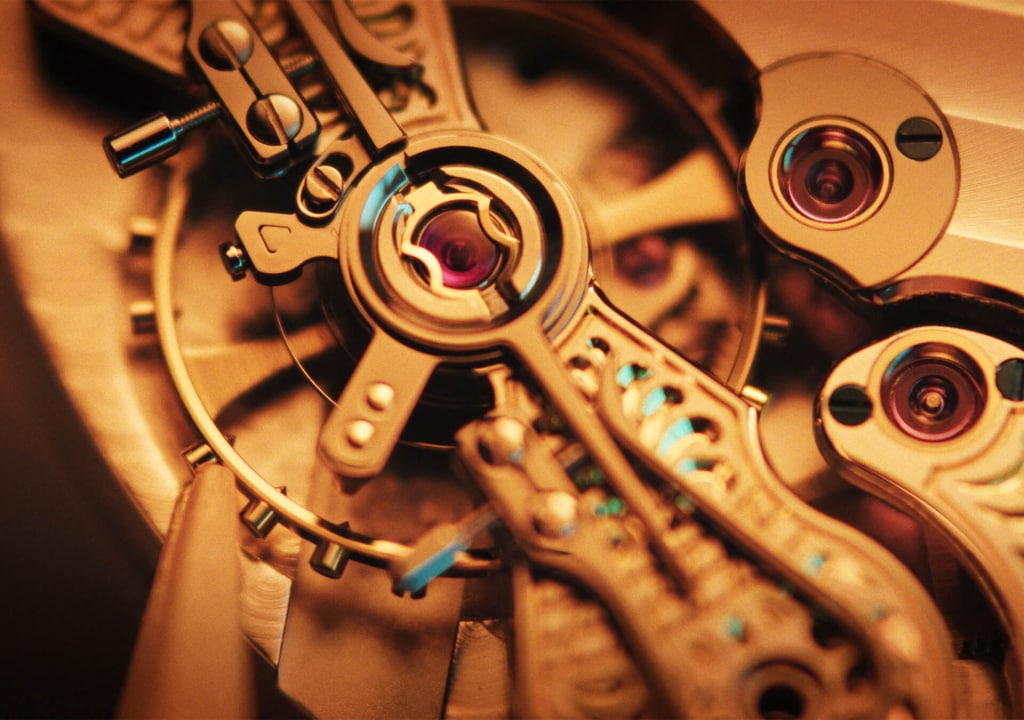
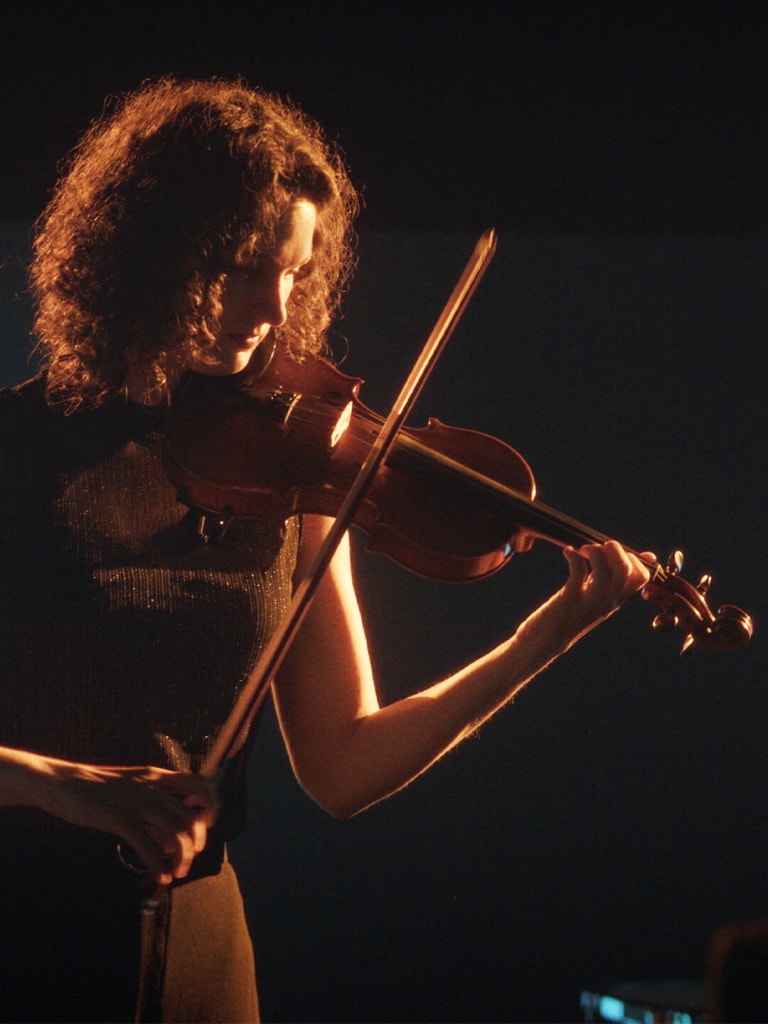
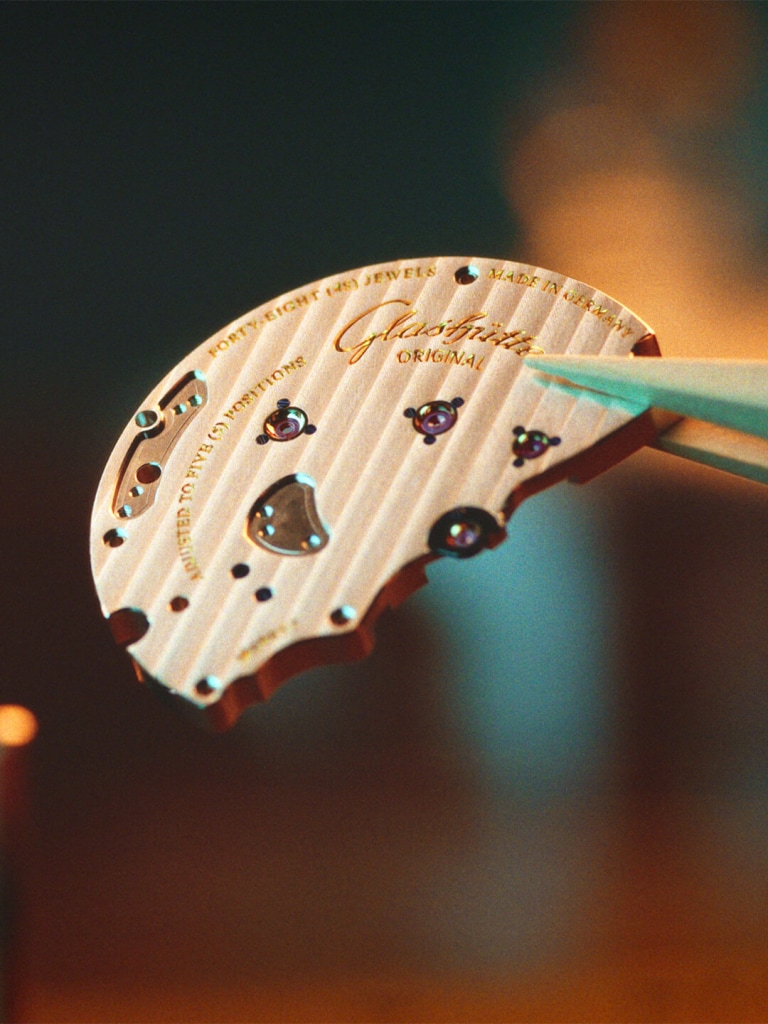
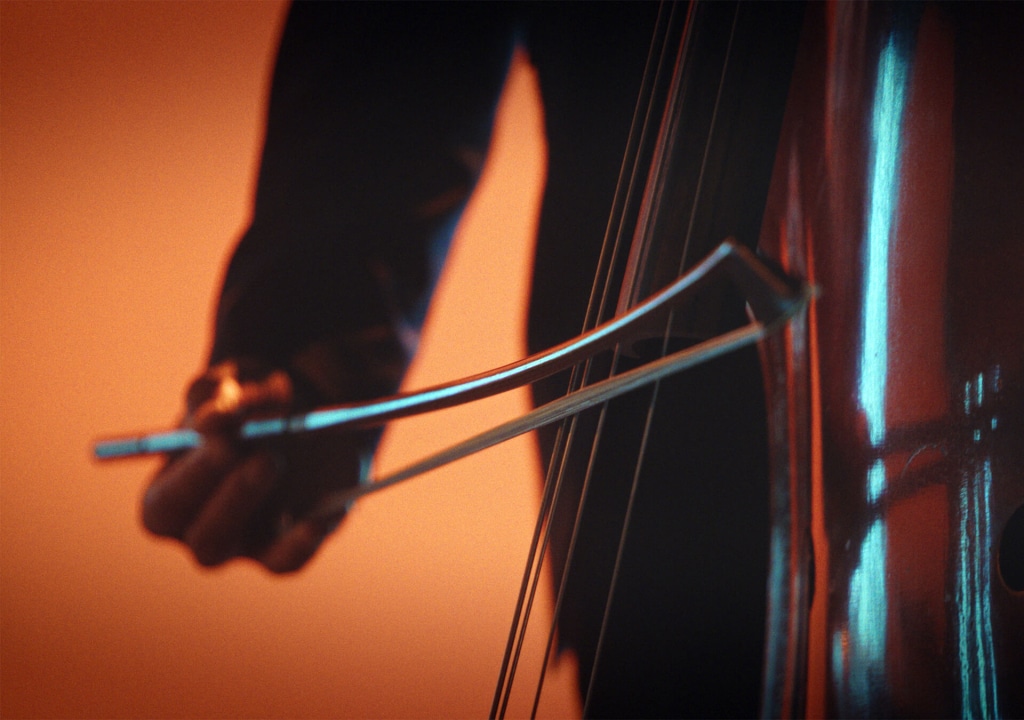
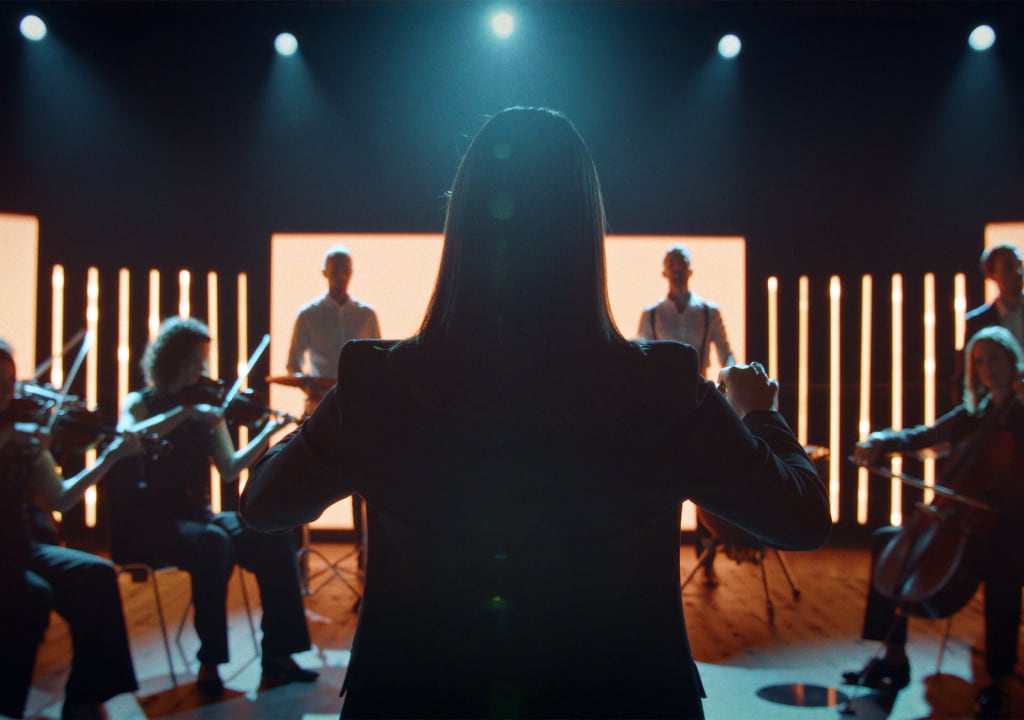
Traditional features
Unlike the Swiss watchmakers, the wheel bridge used in Glashütte watchmaking since 1864 covers three-quarters of the movement’s surface. It houses all the movable parts, from the spring barrel to the escape wheel. This ensures a much more stable construction of the movement.
The balance is part of the oscillation system, comprised of the balance wheel, balance shaft, double roll with plateau and balance spring. With its oscillations and in combination with the escapement system (anchor, escape wheel) it regulates the rate of the watch as well as the operation of the gear train. The balance wheel is set with tiny screws, which serve different functions depending on the regulation system. This complex and decorative construction is a characteristic feature of the fine art of watchmaking and evokes the constant striving of Glashütte’s watchmakers to achieve exceptional precision.
The swan-neck fine adjustment has been a typical feature of Glashütte watch construction since 1888: To regulate the watch, one turns an adjustment screw on the swan-neck spring. It influences the balance spring by means of the regulator. Changing the position of the regulator changes the effective length of the spring, and thus regulates the rate of the watch.
This refined, regular decorative finish has been a characteristic feature of the art of watchmaking in Glashütte from the beginning and is applied with great care to the gear train bridges, the winding rotor and selected balance cocks. Its extremely precise parallel stripes confer a sophisticated finish and optical depth.
The Glashütte sunburst decoration dates back to 1868 and embellishes round and flat components that rotate while performing (ratchet wheel). Subject to the angle at which light falls on the gears, it is reflected in circular patterns, which can have a strong, even hypnotic effect.
Perlage is a typical Glashütte surface decoration of the base plate. It consists of overlapping, pearl-shaped circles that are made by a rotating rubber peg covered with a special diamond powder that is applied to the surface by hand. This gives the movement an unmistakable „pearl“ structure.
Characteristic elements down to the smallest detail: each of the hand-engraved cocks and balance bridges are unique. This comprises engraving a design onto a minute space without the use of a pre-stenciled pattern. The balance cocks and bridges may be decorated only to the extent that the engraving does not interfere with their function.This results in authentic, one-of-a-kind works of art.
On some movements in the prestige watch segment, pivot bearings, or jewels, are set in so-called gold chatons. The chaton is a bed made of 18-karat gold that is placed into special drillings in the wheel bridge and secured with two or three blued screws. Each chaton is fitted in height to its mounted position.
Tiny steel screws mirror-polished by hand turn their colour from grey to yellow, brown, red, and violet tones when heated (tempered) and achieve the desired, permanent deep blue colour at about 290°C. Beside a beautiful deep blue colour, the screw receives a protection against corrosion by polishing.
Traditional horological process where the edges of processed metal surfaces are manually bevelled to an angle of 45°. The bevelled edges must exhibit a constant width and maintain its angle. This process creates decorative, shiny edges, but also a more resistant material by densifying the surface.